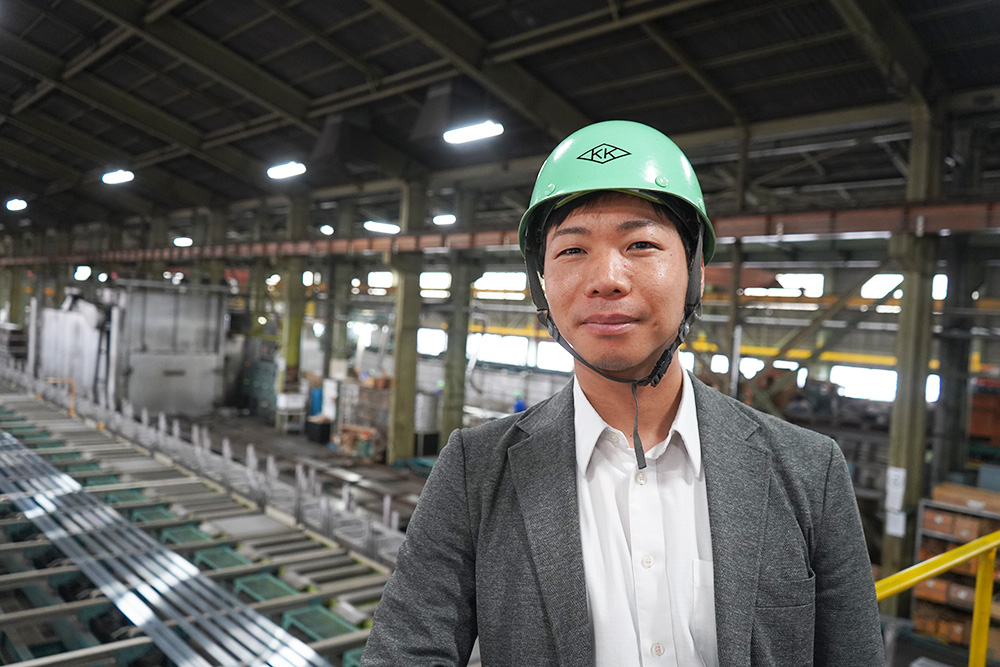
飲料缶やスマートフォンをはじめ、自動車、新幹線、飛行機まで、私たちの暮らしのあらゆる場面で使用されているアルミニウム。軽くて丈夫、しかも熱伝導率が高く加工もしやすい等、様々なメリットを持つ優れた金属である。
昭和36年創業以来、このアルミニウムの押出型材製造及び加工を行っているのが、愛知県海部郡に本社を置く「加藤軽金属工業株式会社」だ。
今回、3代目取締役社長として会社を牽引する加藤大輝氏に、アルミニウム業界の中でも注目を集める自社のSDGsの取り組みについて、その経緯等も含めお話を伺った。
若き3代目が決意した社内改革とSDGsの取り組み
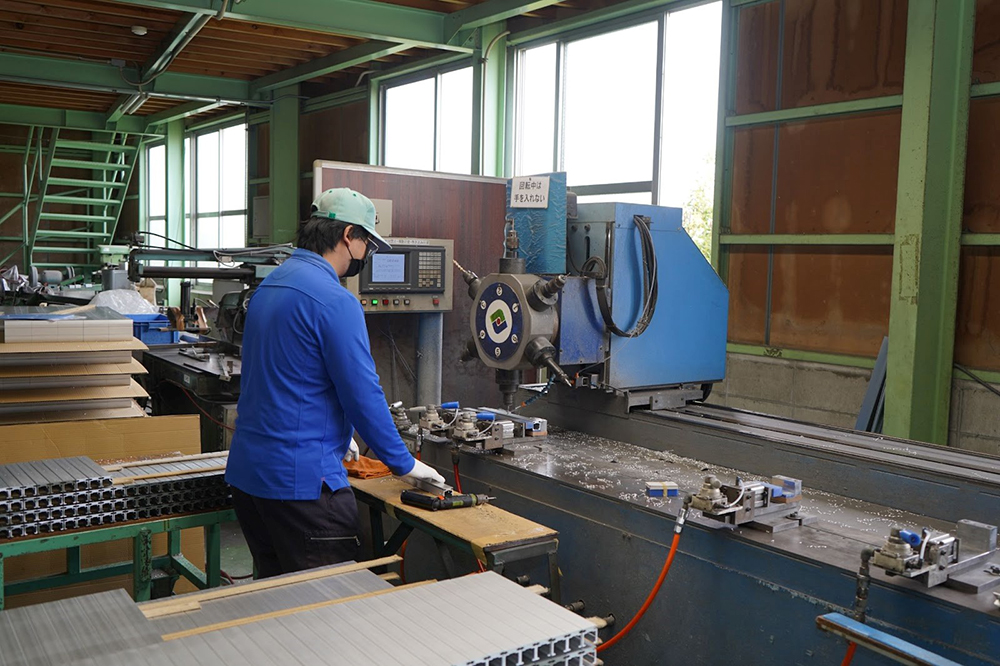
顧客の要望に即し、建材、機械部品、電機、輸送機器、その他オフィス家具等に使用されるアルミニウム合金を月500トンのペースで生産している「加藤軽金属工業株式会社」。
「大切なのは、今あるものに付加価値を付けていくこと」
その使命の下、大型の押出型材製造だけではなく20kg程の小ロット受注にも対応し、併せて切断、加工、組み立てまで提案するという「付加価値」を生み出すことで顧客ニーズに寄り添う姿勢を貫いている。
加藤社長がこの会社に入社をしたのは2020年、社長に就任したのは2023年。
大学を卒業後、経営課題解決を支援するコンサルティング会社に勤務し、父親が立ち上げ成長させてきた会社を継ぐつもりは全くなかったという。
だが、製造業界不況の煽りはそれまで業績拡大の勢いを保っていた自社にも影響を及ぼし始め、徐々に利益が減少。そのことは経営に関わっていなかった加藤社長の目にも明らかだった。
「これ以上、見て見ぬ振りはできない」
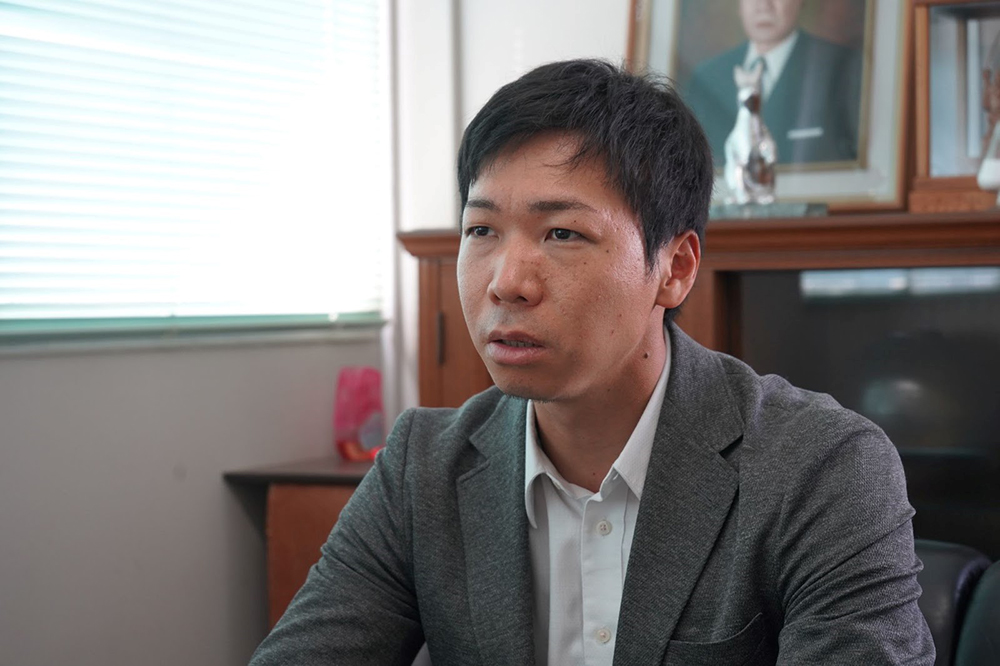
会社を継ぐ覚悟を固め、会社の財務状況を徹底的に調べ上げたところ、結果は予想を遥かに超えるものだった。
あると思っていた貯蓄は減り続け、既に債務超過に。原価計算すら行われず利益率が定かでない受注の繰り返しが主な原因で招いた状況だった。
しかも社内に目を向けると、社員は優秀な人が多いのに、整理整頓はおろか掃除も行き届いておらず、従業員のモチベーションを維持できない環境。さらに個々に腕のある従業員同士の対峙が原因となり生産性が悪化していることもわかり、仕組み作り、意識改革が急務であることも判明した。
その第一歩として取り組んだのが、管理職向けの研修だ。外部講師を招き、一人ひとりが問題意識を持って、「会社としての指針や方向性」を見極め擦り合わせていく勉強会を重ねた。
次第にそれぞれの意識が変わっていき、コミュニケーションも闊達になってきた。そして、2023年4月には会社としてのミッションビジョンバリューを策定するまでに。
寄り添い型探しというMissionを掲げ、お客様に寄り添い・社員にも寄り添う会社、感動や真心、感謝などを軸とした経営に踏み出した。現在ではそのMVVが会社の武器として従業員にも根付いてきていると言う。
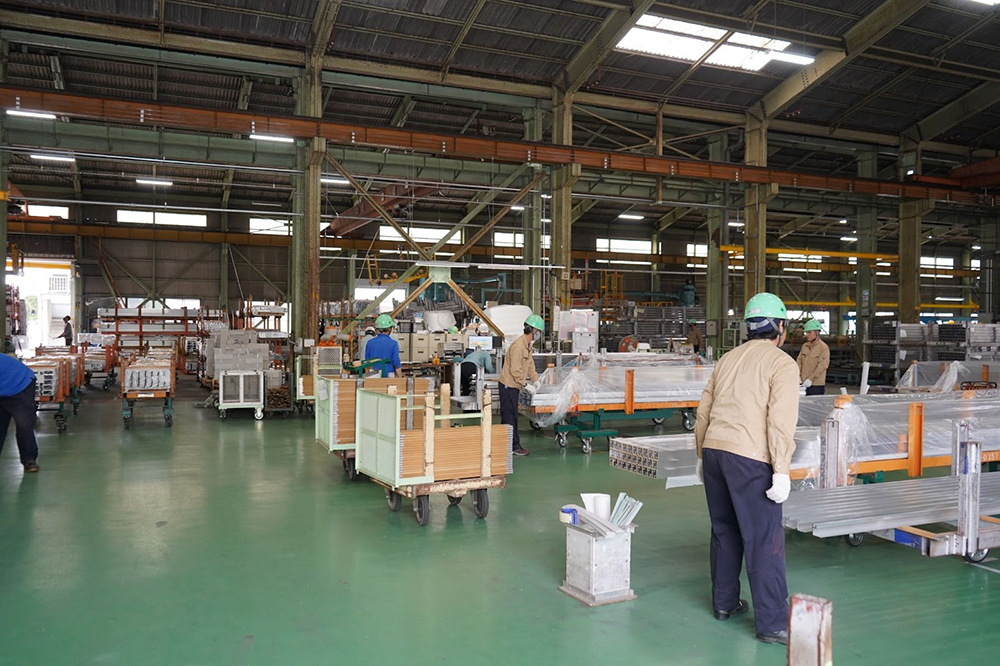
そして遂に、最重要課題である経営の立て直し。
それまでの業務を全て一から洗い直すと同時に、新規事業にも打って出ることに。
そこで始めたのが「SDGsの取り組み」である。
温室効果ガス排出削減からカーボンフットプリント発行へ
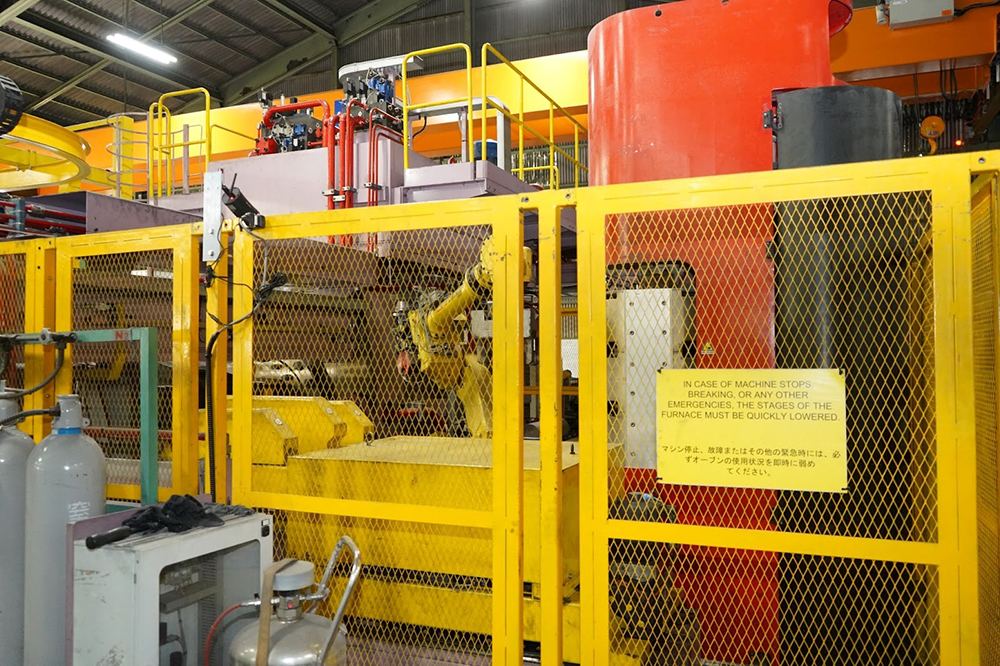
まず、アルミニウムの原料調達や製品製造、販売、消費、廃棄などの一連の流れの中で発生する温室効果ガス排出量「サプライチェーン排出量」を構成する、Scope1(燃焼によって直接的に排出される温室効果ガスの量)とScope2(供給される電気の使用に伴って排出される温室効果ガスの量)への対策として「省エネ」を考慮し、従来の装置をイタリア製直接横型押出機へと入れ替えた。
通常、アルミニウムの原材料ビレットはハロゲンヒーターのような熱源を利用して約500℃まで温めなければならないが、そこに新たな装置を用いることで熱伝導効率が30%程度アップ。使用電力量が減少した。
それと並行して、太陽光パネルでの自家発電にも踏み切ったことで、さらに消費電力の削減に繋がっている。
また同時に、省エネ診断としてCO2排出量の削減可能性を数値化した上で、実際に工場内の各装置の使用電力及びCO2排出量を「見える化」。
日々の生産データを計算することで、電力原単位を把握できるプラットフォームが構築され、併せてScope3(Scope1、Scope2以外に間接的に排出される温室効果ガスの量)も明確にし、改善効果も可視化出来る状態になっている。
次年度には、材料調達から廃棄・リサイクルに至るまでのライフサイクル全体を通して排出される温室効果ガスを算出し、「カーボンフットプリント」も発行する予定だ。
SDGsの鍵は「グリーンアルミニウム」と「再生アルミニウム」
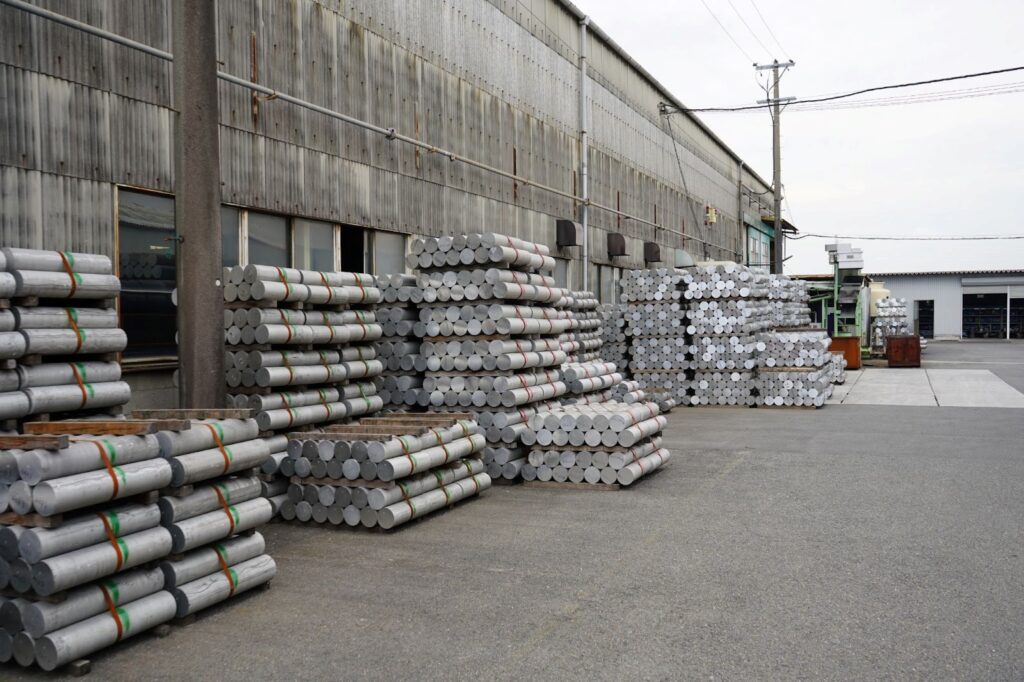
SDGsの取り組みとして今後さらに注力していきたいのが、「グリーンアルミニウム」の使用だ。
「グリーンアルミニウム」は、製造する際に化石燃料を用いた火力発電ではなく、水力、風力、太陽光等の再生可能エネルギーを用いている。従って、通常の新塊アルミニウムに比べ90%近くCO2削減が可能となり、地球環境に優しい重要な取り組みと位置付けている。
ただ、現時点では水力由来のグリーンアルミニウムが高単価になってしまったため、普及にはまだまだ課題があり、高級モデルなどブランド力がある高価格商品にしか導入できていない状況である。
一方、製造工程で発生するアルミスクラップから再生ビレットを鋳造した「再生アルミニウム」は、水平リサイクルが一般的で数十年前から利用されている。新塊アルミニウムと比較した場合のCO2 排出量は 1/30と環境への負担も少なく、高単価である「グリーンアルミニウム」よりも「再生アルミニウム」を使う流れが主流になりつつある。
だが現状として、日本国内よりも海外の方がスクラップを高く購入するため、国内から海外へとアルミ材が流出している。今後、国内で再生されない状況が続けば、CO2負荷が高い新塊アルミニウムを買い続けなければならず、アルミ利用製品の競争力低下に繋がるとも言える。
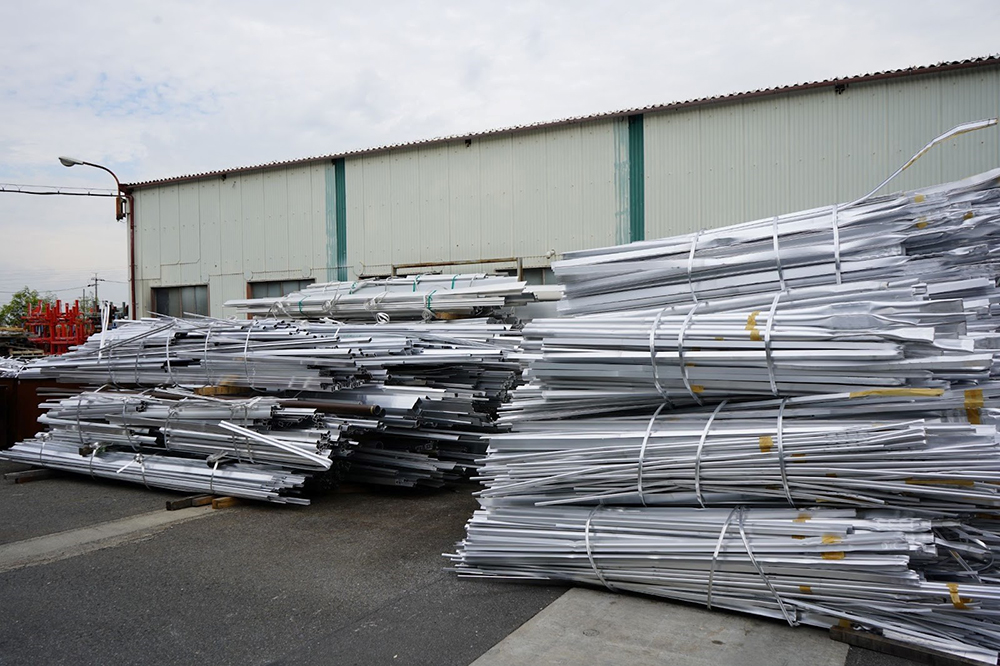
そこで現在、新たに構想しているのが「アルミ再生炉」の企画である。
CO2削減も念頭に置き、複数の企業と共同で回収から再生、さらに再提供までのスキームを確立させ、国内の製造業が再生アルミニウムを使用できる流れを作る予定だ。
さらに取り組む、2024年問題への対策とベンチャーとの共創
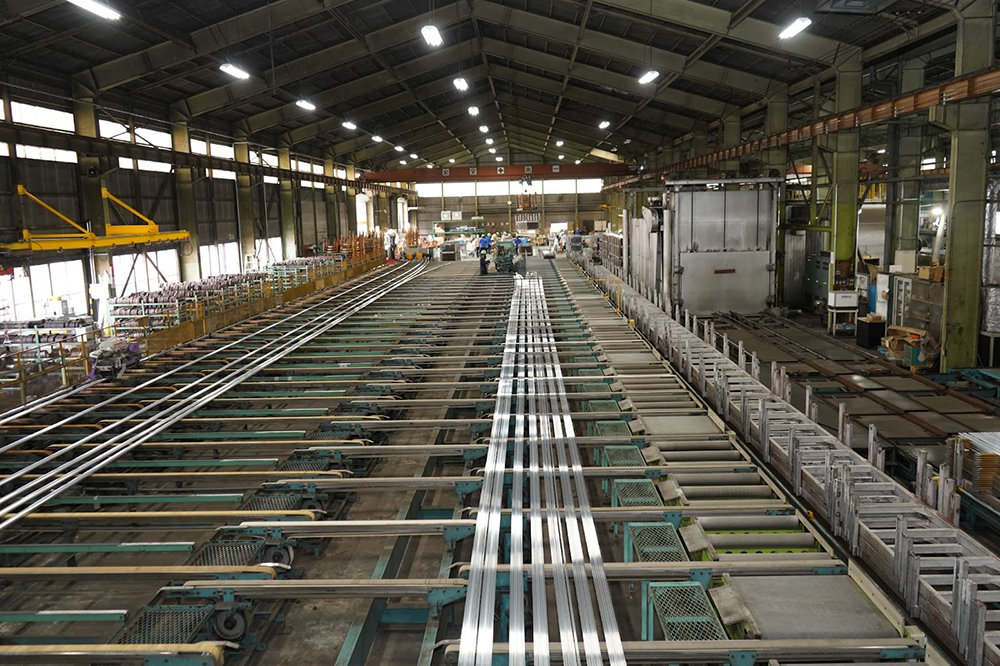
運送業界の2024年問題に対しても、新たな一手となる「共同運航便計画」を進行中だ。
4m、6m、8mといった長物の型材輸送が多いアルミニウム業界にとって、運送効率の悪さは長年の課題だった。
そこで考えたのが、鉄鋼業界全体を巻き込み、アルミニウムだけではなく鉄等も共同で出荷することにより可能な限り満載で輸送、積載効率を上げるという計画だ。
現在、地元の商工会議所や大手輸送会社の協力も得て、複数社による共同会社(SPC)を設立予定。当然これによる温室効果ガス排出量削減も見込んでいる。
加藤社長は三方良しの理念から、ベンチャー企業と提携し、その事業を社会実装させていく取り組みも重要と位置付けている。
冒頭でも触れた、5~20kg程の小ロットアルミビレットの受注にも対応していることもその一つだ。新素材開発などにおいて、従来のような多額のコストや自由度の低さを回避することでベンチャー企業を支援し、細かな要望に応える個社戦略を実践している。
さらに、全固体電池・レドックスフロー電池のベンチャー企業や金属と樹脂の接合技術のような自社では研究開発が難しい分野に取り組むベンチャー企業と共創することで、それらの技術のコモディティ化も図ろうと注力している。
最重要ミッションはお客様に寄り添うこと
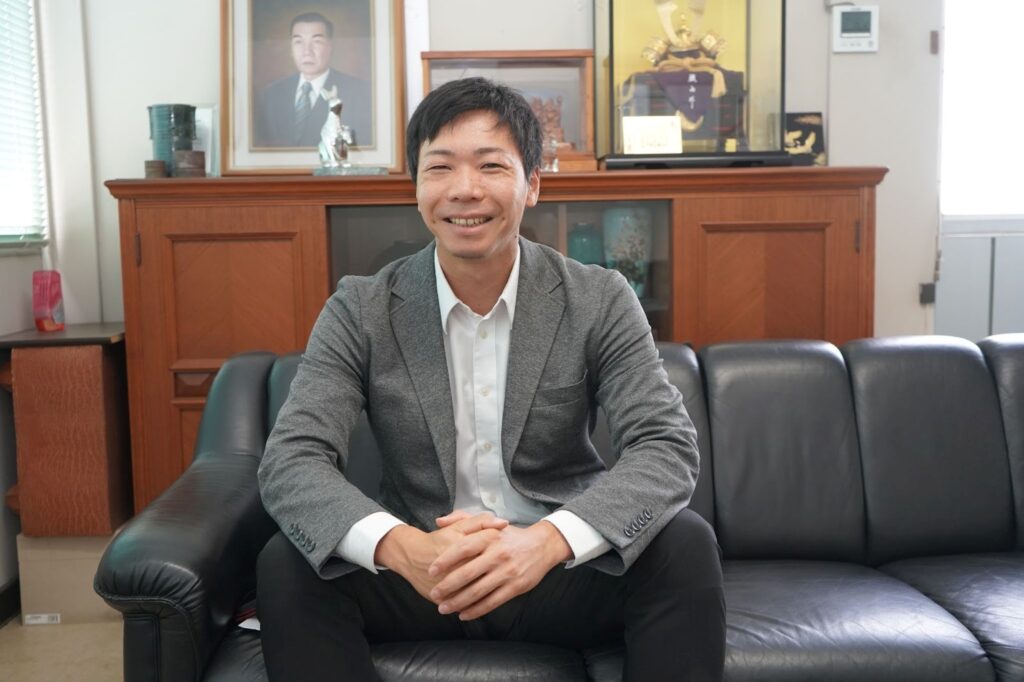
このように会社継承以降、財務や事業の見直し、新規事業の開発、従業員の意識改善等、様々な改革に取り組んできた加藤社長。
現在は、アルミニウム業界全体として、再生に関してのCO2排出ルール策定や先述の2024年問題等の課題解決を図っていくことも必要だと感じている。
まずは、先日任命された「一般社団法人 日本アルミニウム協会」の理事として、積極的にその任を果たす考えだ。
「個々のお客様に寄り添い、ご要望に応える」
このことを今後も最重要ミッションに据えていきたいと語る加藤社長。
商品開発、新たな材質への対応、さらに押出加工後への付加価値提案等にも意欲的に取り組んでいきたいと考えている。
目指す会社像を実現するまでには、まだまだ道半ば。だが、短期的、中長期的なビジョンに向かい、全従業員と共に一段ずつ着実にステップを踏んで行きたいと決意している。
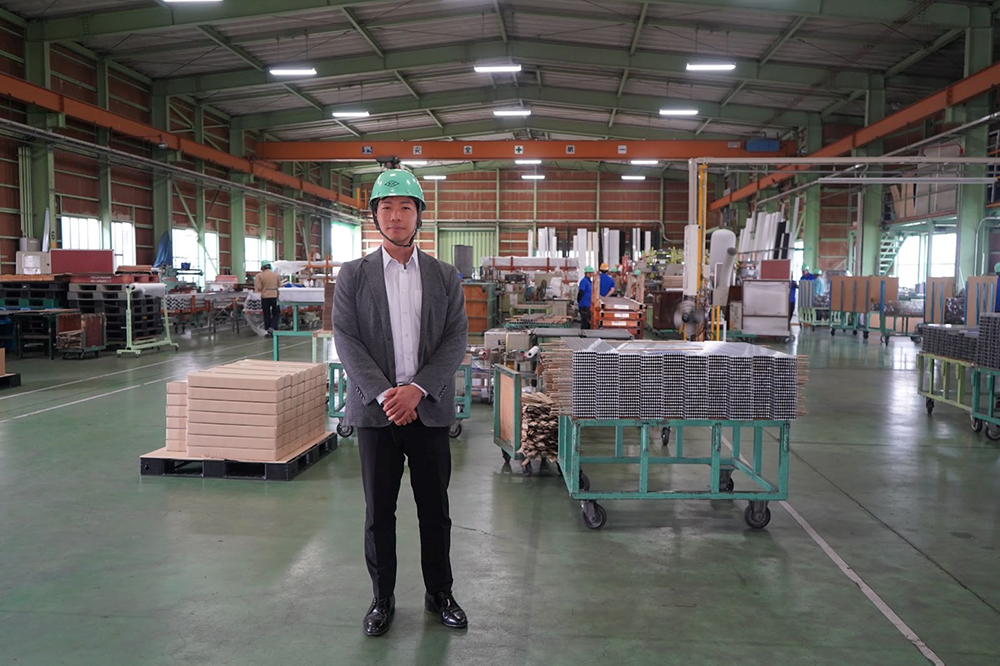
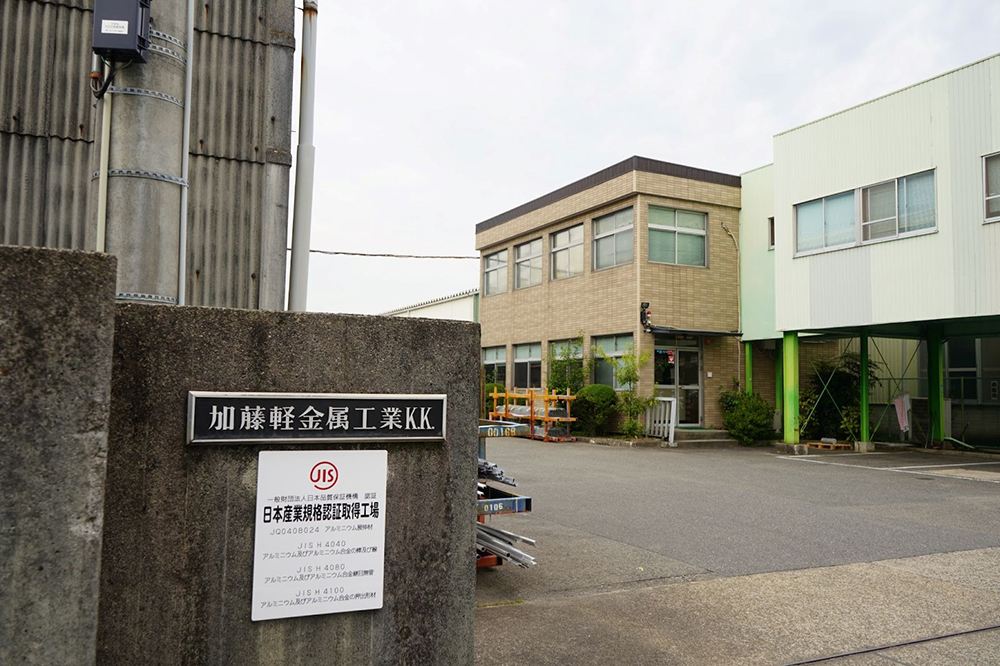